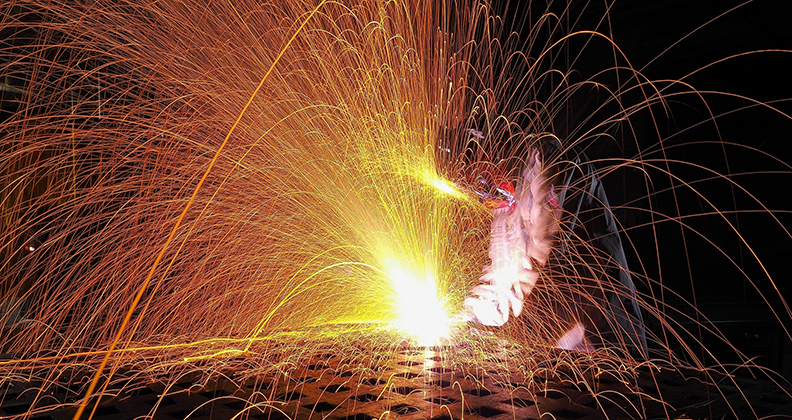
Without one, manufacturers have relied on welding specifications for other industries, such as aerospace. Those requirements, however, often focus on parameters that are either insufficient or unnecessary for medical devices, said Clayton Martin, a process engineer who is spearheading the welding specification initiative taskforce.
“One of the difficulties is that historically, medical device companies have applied different specifications, including internally developed methods, for welding. This has led to significant inconsistencies regarding weld requirements for the industry,” the taskforce told us in a collective interview. “A specification that captures the science of welding, incorporating the specific needs of medical devices, has been needed for some time.”
An industry-recognized engineering and welding specification for medical devices would address several challenges. For example, it could identify whether a professional has the qualifications to perform a weld and whether a weld is meeting the specified requirements.
“While there will always be highly specialized weld challenges that may exceed the capability of a weld specification to mitigate, the vast majority of welds being performed will benefit greatly from the development of this specification,” the taskforce said. “How critical is a specific weld? How do you evaluate that weld according to that criticality? What critical variables need to be considered when developing a weld? We seek to answer these questions within the context of medical devices, given the specific constraints and concerns for a positive patient outcome.”
Specialized for Orthopedics
As the taskforce develops the new welding specification, they are utilizing specifications that are commonly referenced within the industry as foundational elements, including specifications for aerospace, pressure vessels, food, dairy, pharmaceutical and structural steel. These have nearly 100 years of historical case studies and development to their credit.
Initially, the taskforce will be focused on orthopedic instruments, which is where the majority of welding is done within the industry.
“It is recognized that there will be a need for future developments, and it is expected that this effort will provide a foundation for those efforts,” the taskforce said.
Industry-Wide Collaboration
As a topic that affects manufacturers throughout the industry, the welding specification initiative taskforce comprises several representatives from six OEMs, three contract manufacturers and others, including standards and regulatory organizations. These are competitor companies and vendor/partner companies coming together to address common problems.
Ivy Tech Community College of Indiana has provided a forum for the taskforce’s meetings, has played an integral role in conversations between the taskforce and outside organizations, and will assist in educating students and industry to the spec once it’s published, Martin said. Long-term sustainability and progression of the welding specification must include a vocational element of training, he added.
“Welding is a science that is often misunderstood,” the taskforce said. “No single entity should be creating a specification of this nature; it must be consensus development work. This is a cross-functional group with orthopedic OEMs, weld houses, manufacturers and educators. There was a consensus in recognizing the need for a standardized list of requirements for welding medical devices. Our focus has always been patient safety.”
The companies involved in the taskforce will be named upon publication of the engineering specification. There is not an estimated timeframe for when the specification will be released, as it remains in development and will undergo a lengthy review process through a consensus standard development methodology.
HT
Heather Tunstall is a BONEZONE Contributor.