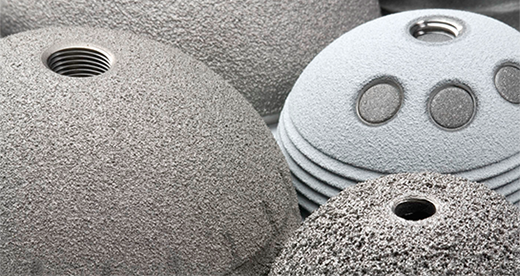
As the orthopaedic industry has evolved, so too have coatings for implants and instruments. BONEZONE queried five companies to better understand trends in coatings, as well as ways that device companies can work with suppliers to adapt new technologies and overcome regulatory and cost barriers.
Participants:
Parimal Bapat, Ph.D, Research Engineer, Orchid Orthopedic Solutions
Ulf Brogren, CEO, Promimic
Céline Harnisch, Marketing and Technical Support, Alhenia
Richard Vandevelde, Founder and President, MedicalGroup
Tim Zentz, Sales Manager, Danco Anodizing
BONEZONE: What trends in coatings do you see in devices used in the orthopaedic industry?
Parimal Bapat, Ph.D.: While most OEMs still heavily rely upon traditional coatings, such as sintered bead and plasma sprayed metallic coatings, more customers have shown interest in coatings that have certain surface properties, such as high roughness, interconnected porosity, etc. There is a growing interest amongst customers for 3-D printed implants, which allow one to design and build an entire implant with the coating in one single process. As far as the hydroxyapatite (HA) coatings, customers still heavily rely on traditional plasma sprayed HA coatings. There have been requests from customers to develop solution-based HA coatings that will allow one to have the HA coating inside of the porous structures, which is not possible with plasma sprayed HA coating.
Ulf Brogren: Product differentiation will be key to success in many implant market segments, because the majority of implants currently available on the market have similar designs and functions. Also, as the market shifts due to changing demographics and growing health problems, the demand for high-performing implants is increasing. Combining novel implant designs with coatings, adding the right bone chemistry for better and faster integration, will be one important solution to these problems. Promimic sees an increasing demand in coatings from these marketing and clinical perspectives.
Within the spine segment, development teams of the leading spine implant companies seem to be evaluating coatings of PEEK-interbody devices at this moment. The reasoning for this is to create devices that actually integrate with bone, in order to support a better and faster fusion.
Céline Harnisch: Nowadays, coatings are accepted and widespread in the medical field. Various new applications with different processes have developed, such as new coatings techniques and new materials to be coated. Innovative coatings were also brought to market, offering anti-infective solutions for orthopaedic implants. In this way, antibiotics or biofilms are deposited onto the coated surface.
Richard Vandevelde: When I started MedicalGroup 25 years ago, our two core businesses were plasma spray coatings and HA manufacturing. At that time, very few implants had porous coatings. Nowadays, more implants have porous coatings. These implants are found throughout the different markets, such as extremities, spine, dental and even trauma, in addition to the traditional hips and knees. The goal is to create bone attachment to the implant and quicker bone generation, which will increase the stability and life of the implant and therefore drastically decrease revision rates. Also, all types of substrates can now be coated: Ti, SST, CoCr, PE and PEEK.
In addition, we have noticed that larger OEMs are integrating plasma spray coating capabilities, either for HA or titanium. Their goal is to control this very specific process by being their own first or second source.
We help our customers with those two issues. First, by providing surface treatment services (Ti and HA plasma spray coatings, RBM, low temperature deposition of HA) on orthopaedic, spine and dental implants. Second, we manufacture HA and titanium powders. We handle plasma spray coatings and supply the powders, allowing us to assist our customers with their coating specifications, equipment set-up and validation.
Tim Zentz: Although some feel that coatings are cost drivers, we feel that there are trends where organizations can realize potential cost savings when evaluating increased performance or increased life expectancy of a product when coatings are applied. Coatings such as Type 2 titanium anodizing, per AMS 2488, will increase fatigue strength, add lubricity and improve surface finish. In addition, Danco’s Low Friction Chrome Coating process, per AMS 2460, for stainless steel instruments will increase the life of an instrument through added corrosion resistance, lubricity and increased hardness.
BONEZONE: What challenges do your OEM customers report with coating technologies? How do you help?
Bapat: One of the bigger challenges OEMs have is the FDA regulatory path for coating technologies. FDA relies on ASTM for developing new test methods
FDA has guidelines for traditional coatings, but doesn’t have guidelines for new coating technologies. When one develops a new coating, one has to conduct tests that are applicable to traditional coatings or has to adjust the test according to limitations of the coating technology. In general, what FDA looks for is the third-body wear risk and biocompatibility of the coating.
Orchid has vast experience with both FDA and ASTM, hence it becomes easy for us to serve the customer per their need.
Brogren: Regulatory questions always top the agenda. This is followed by the overall drive to decrease production costs. Third, complex logistics and shipping of implants is always a struggle.
Our unique wet chemical coating process can be implemented anywhere an implant is produced. Through a licensing agreement, the OEM gets full control over the coating process directly at their production line. The Promimic coating technology can coat all kinds of shapes and materials in a cost-efficient way, and we are working with FDA to establish predicate devices and master files for our HAnano Surface. Furthermore, Promimic has developed an extensive portfolio of pre-clinical in vivo data that may facilitate and support customer regulatory submissions.
Harnisch: As the field of application for coatings becomes larger and larger, we assist in different challenges:
- New materials for biomedical applications have appeared on the market in recent years (PEEK, for example). According to this evolution, we have to conform to our customers’ requests and develop coatings on new materials.
- Coatings are in constant evolution. Taking this into account, we strive to develop coatings that meet the best criteria to enhance cell proliferation and thus osseointegration. In this, porosity and roughness are the main parameters at play.
- Much attention is focused upon wear resistant coatings. Indeed, the worn particles can collect in the tissue surrounding the joint, causing osteolysis and subsequent joint failure by loosening.
- The apparition of new markets allows us to expand worldwide. A big challenge for our company is to introduce our products and adapt to the regulations applied in these countries.
In order to help our OEM customers, we constantly develop new applications mastering the latest surface engineering technologies. Our core technologies consist of Vacuum Plasma Spraying (VPS), Atmospheric Plasma Spraying (APS), Cold Gas Spraying and Physical Vapor Deposition (PVD).
Vandevelde: Only large OEMs have sufficient technical and financial capabilities and volumes to integrate plasma spray coating. Mid- and small-size companies and large OEMs not completely integrated want a turn-key solution for their implants and want to limit their number of subcontractors. In response, MedicalGroup has integrated complementary services to our two core businesses, such as forging and machining, sterile and non-sterile packaging, lab testing (ISO17025) and synthetic biologics.
Also, implant companies need a manufacturing partner that can help them receive regulatory approval worldwide in order to sell their products in mature markets (U.S., Europe) and developing countries (China, Brazil, Middle East). Our lab and engineering teams have supported many of our customers who are now located all around the world.
Regarding the integration of plasma spray coating, equipment set-up and media selection are key issues. Our expertise in the coating process and manufacturing of custom HA and Ti powders make us a key partner in their set-up and operations.
Zentz: The challenges expressed by the majority of OEM customers lie in process repeatability and expected overall performance. Add to this the growing interest in validations, continued requirement for biocompatibility and proof of “value added” through functional testing. These items are critical. In most cases, Danco has such tests completed or is able to partner with the OEM to fulfill their testing needs.
BONEZONE: Regarding coatings, what one question do you wish your orthopaedic device manufacturer customers would ask you in order to better serve their needs?
Bapat: “What are coating handling instructions?”
Brogren: “How can we increase the integration between our device and bone without adding any new risks with the coating layer?”
Answer: With our super-thin hydroxyapatite surface, we add bone-like chemistry that attracts bone cells and accelerates integration. Since the coating is only 20 nanometers thin, bone will integrate with the implant in the micro and macro roughness of the implant surface and not into the coating itself. This means that even if the coating would resorb or be damaged, there is no risk for implant failure.
Harnisch: The one question would concern the administrative part of the qualification and validation of the coatings and products. According to the customers’ needs, each new product has its own validation with more or fewer tests required. This represents an important issue for coating companies. The best solution would be to standardize the procedure for time and money savings.
Vandevelde: We wish that our customers would bring us on board earlier on in their projects, for the coating process and the equipment set-up. Also, that they would communicate all of the available information that they have regarding packaging, sterilization type, countries in which the products will be sold, as soon as possible. The more we know and the earlier on, the better we can assist our customers with coating and packaging design, as well as regulatory approvals around the world.
Zentz: “Would Danco be willing to consult with us early in the development of new or revised products having significant finishing requirements?”
Surface preparation prior to anodize or coatings is critical. Danco is able to partner with our orthopaedic customers at the RandD and prototype stages by answering their questions regarding the most optimal surface preparation in order to meet their needs. In many instances, Danco is able to process samples at no charge to allow the customer to evaluate physical samples.
BONEZONE: What have we not asked about coatings, that you wish we would?
Bapat: “What is the surgeons’ perspective in developing new age coatings? Are surgeons looking for something specific in the coatings?”
It’s hard to tell what surgeons are looking for, as contract manufacturers rarely talk directly to the surgeons. Having said that, one of the requests that we hear from OEMs is for rough titanium coating.
Brogren: “During the last five years, porous implant materials have been established as a solution to integration problems. Will the demand for coatings decrease as the porous materials become more common?”
Answer: No; instead, we believe that the use of porous implants will result in an increased demand for new types of coatings—those that can be combined with porous materials. Such coatings will be based upon wet chemistry without the need for line of sight, adding bone chemistry and bio-mimicking nano-structures to the implants without clogging the pores. This will create implant materials that are structured as bone and have a bone-like chemistry. This is an example of the high-performing implants that will be required to meet the increasing clinical demands, as more patients will need implants due to poorer bone quality.
Harnisch: One point that could help for the coating process is enhanced knowledge about medical coatings by design engineers. Thanks to this, they could adapt the implant’s design to the process and avoid coatings companies a lot of preparation work before coating.
Vandavelde: “As a specialist of HA powder manufacturing and HA coatings, what is your opinion on its uses and future?”
Answer: Studies over the past 30 years have proven the advantages of HA plasma spray coatings on implants to speed up bone growth. Therefore, it is widely used and recognized in surface treatments in developed and developing countries and regions such as Europe, Middle East, Turkey, China and India. HA is used in various surface treatment applications such as:
- Single or double layer plasma spray coatings
- As a fully resorbable blasting media (RBM) to create roughness (1 to 3µm) on dental implants. It has the advantage of being 100 percent cleanable and therefore leaves no residual particle, which is different than other blasting medias like aluminum oxide
- Thin layer deposition at lower temperature on additive manufactured implants. This process allows an even deposition of HA (10 to 30µm) deep into the porosity of the implants. It can also be applied on other implants of all sizes and shapes.
- As a powder to manufacture individualized 3-D implants mainly for maxillofacial applications
- And finally, in synthetic biologics