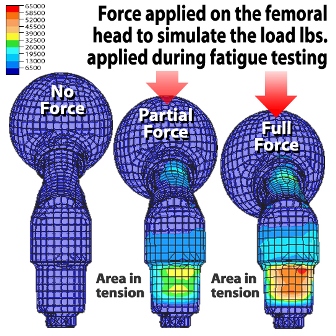
Introduction
The demand for total hip replacement surgery has risen dramatically for the last decade. If rates continue to grow, the annual number of surgeries will top 600,000 by 2015.1 The use of titanium modular implant systems is popular with surgeons because it allows for precise fit to the patient with a less invasive surgical procedure. However, modular prosthetics can be prone to fretting damage at the contacting surfaces of the tapered connections between subcomponents. Surface micro-cracks, caused by shear stresses at the contact surface during fretting, can lead to a reduction in fatigue strength that significantly reduces the functional life of the prosthesis. Implanted hip systems experience a spectrum of cyclic loading from normal day-to-day patient activities that can cause the micro-cracks to propagate. Further, risk of failure is affected by a patient’s size and level of activity. Implant failure leads to revision for the patient, and the possibility of litigation for the prosthetic providers.
Manufacturers have tried to offset these issues by creating hips out of nickel, cobalt and chrome alloys, intending to offer a stronger implant that is less prone to failure. Recent research has demonstrated that these materials have severe problems with biocompatibility. For example, 30% of patients with hips made from these alloys suffer from hypersensitive metal allergy. If the hip begins to fail, this number jumps to 66%.2
Adding a layer of residual compression to a metallic part has been shown to slow or even terminate fatigue crack initiation and growth.3-6 Traditional methods such as shot peening have been used across industries to add a protective layer of residual stress to components, but some of these carry serious issues for use on medical devices. They may not provide the depth of compression necessary to offset fretting damage in modular hip implants. These surface treatments can also produce a rough surface that prevents their use on precision tapered joints, and can leave behind residue which can lead to contamination of processed pieces.
Low Plasticity Burnishing (LPB®) has been developed by Lambda Technologies to impart controlled residual compressive stresses in metal components to increase damage tolerance and improve fatigue life. LPB creates a deep, stable layer of beneficial compressive residual stress in the component surface without introducing damage. This protective layer of compression suppresses fatigue cracking from flaws shallower than the depth of compression making the piece resistant to a variety of damage, such as machining marks, handling damage, stress corrosion cracking, corrosion pitting and fretting.7
LPB was initially applied and proven to eliminate fretting fatigue failures at the dovetail joints of titanium alloy (Ti-6Al-4V) jet engine compressor blades, the same alloy that is used in hip prostheses. Review and acceptance by the FAA for use in commercial aircraft supported extending the application of LPB to solve the similar medical prosthesis fretting problem. The deep compressive surface layer suppresses fatigue initiation and crack propagation from the fretted surface, while producing the high quality surface finish needed for the tapered joints.
LPB and Replacement Hips
In 2006, Exactech began searching for a new way to mitigate fretting-initiated fatigue. During a continuous improvement assessment for the Exactech M-Series modular hip prosthesis, it was hypothesized that the controlled application of compressive residual stresses to the taper joint surface could improve fatigue strength. The possibility of using residual compression to extend life offered important advantages, including maintenance of the existing material and design that already had FDA clearance.
After experimentation with conventional roller burnishing and research into laser and shot peening, the LPB process was identified as the most promising surface treatment method for fatigue strength improvement. An LPB process and tooling were designed to improve the fatigue strength and fretting damage tolerance of the M-Series modular hip prosthesis.
Using finite element modeling of the applied stresses and a patented fatigue design protocol,8 a custom residual stress field was created for the application of LPB to hip implants. Exhibit 1 shows the real life loading conditions that were simulated on a model to obtain the stresses applied in service and determine the required depth of compression. Several factors needed to be taken into account: equilibrating residual tensile stresses, dimensional changes and the cost of processing. Exactech had to be sure that the surface enhancement treatment chosen would not simply move the location of maximum stress, weakening another section. LPB prevents this by evenly dispersing the equilibrating tensile stresses. Component dimensions had to be maintained because of the tight tolerances of the tapered joint of modular hip implants. LPB processing was developed so that the critical dimensions in treated parts were maintained. The complete LPB stress field can be seen in Exhibit 2.
Exhibit 1: FEA showing applied forces in normal use
Exhibit 2: FEA showing LPB treatment
Life Improvement
High Cycle Fatigue (HCF) testing was performed on untreated (baseline) and LPB-treated hip stems to demonstrate the performance improvement. Tests were run in accordance with the appropriate ISO 7206 standards.
Baseline specimens were tested within a load range of 1,050 to 1,400 lbs. All fatigue failures in baseline specimens occurred in the fretted tapered neck region of the hip segment. Baseline results indicate a fatigue strength at 107 cycles of 1,050 lbs. LPB processed neck segments were tested in a higher load range of 1,400 to 1,600 lbs. to produce any failures. Full results are detailed in Exhibit 3. LPB improved the fatigue strength of the hip stem more than 40% and increased the life by 15x, as shown in Exhibit 4. No failures initiated in the fretted LPB processed neck taper region.
Exhibit 3: High Cycle Fatigue Data
HCF results indicating LPB produces a 40% increase in fatigue strength at 107 cycles. Arrows indicate run-outs.
Exhibit 4: Life increase from LPB Treatment
Transition to Production
After verifying that LPB was the right surface treatment for their prosthetics, Exactech began to implement it into their manufacturing process. Exhibit 5 shows the treated area on a hip as it would be installed in a patient. LPB operates using basic CNC code and is easily installed on existing machinery, such as lathes and milling machines during machining, or on robots. Processing can be done on either a dedicated unit or by simply changing tools on the same CNC machine used for manufacturing.
Exhibit 5: Diagram illustrating hip placement and LPB treated area
Lambda provided a turnkey LPB machining process for the Exactech manufacturing facility on the same lathe used for machining the implants. The LPB system included the CNC tool control code and pressure files specifically designed for the implant that define the tool position and burnishing force. Exhibit 6 shows the LPB tool installed on a CNC machine. Use of a CNC-controlled tool path is intended to deliver absolute repeatability. LPB processing incorporates continuous, closed-loop monitoring. The computer-operated servo control monitors the burnishing force applied in real time throughout the CNC controlled process, ensuring that each location is treated with the precise amount of force required to produce the designed magnitude of beneficial residual compression. The system provides automatic pass/fail notification for each treated component, and QA personnel are informed immediately by email upon system malfunction or part rejection. Statistical Process Control (SPC) information is collected constantly, and each piece processed can be tracked individually by serial number.
Exactech performed rigorous testing to ensure that LPB-treated prosthetics met FDA standards. Results showed that LPB enhancement did no harm and improved the performance of the modular hip replacement. The LPB process has been fully approved by FDA for production.
Exhibit 6: Hip taper LPB production in a CNC lathe
Conclusions
The beneficial residual compression introduced by LPB treatment into the tapered joints of modular titanium alloy hip prostheses eliminated fatigue initiation from fretting-induced micro-cracking. LPB provided a fatigue strength superior to un-fretted material, and over 50x life extension. The ease of LPB development and processing provides a practical means of reducing the risk of failure or the need for surgical revision while retaining the benefits of existing design and the lightweight, biocompatible titanium alloy.
Since LPB implementation began, Exactech hasn’t experienced a single failure from a processed hip. Other major implant manufacturers have also begun to use LPB. More than 20,000 titanium modular hips have been LPB-treated, and none have failed. By implementing LPB, implant manufacturers can now offer safer, stronger prosthetics without a major increase in cost, and without changing either the prosthesis material or design. Dramatically improving fretting fatigue performance of prostheses with LPB has reduced risk for all parties involved.
REFERENCES
1. Kim, S (2008). Changes in surgical loads and economic burden of hip and knee replacements in the us: 1997–2004. Arthritis Care & Research, 59(4), 481-488.
2. Jacobs J, Goodman S, Sumner D, Hallab N. Biologic Response to Orthopaedic Implants. In: Buckwalter J, Einhorn T, Simon S, editors. Orthopaedic Basic Science. 2nd ed. AAOS; 2000. 401-426.
3. Frost, N.E. Marsh, K.J. Pook, L.P., Metal Fatigue, Oxford University Press, 1974.
4. Fuchs, H.O. and Stephens, R.I., Metal Fatigue In Engineering, John Wiley & Sons, 1980.
5. Berns, H. and Weber, L., Influence of Residual Stresses on Crack Growth, Impact Surface Treatment, edited by S.A. Meguid, Elsevier, 33-44, 1984.
6. Ferreira, J., Boorrego, L, and Costa, J., Effects of Surface Treatments on the Fatigue of Notched Bend Specimens, Fatigue, Fract. Engng. Mater., Struct., Vol. 19 No.1, pp 111-117,1996.
7. Hornbach, D., Prevey, P., & Loftus, E. (2005, 11). Application of low plasticity burnishing (lpb) to improve the fatigue performance of ti-6al-4v femoral hip stems. Presentation delivered at Symposium on fatigue & fracture of medical metallic materials & devices, Dallas, TX.
8. Prevey, P and Jayaraman, N. (2005). A Design Methodology to Take Credit for Residual Stresses in Fatigue Limited Designs. Journal of ASTM International, Vol.2, Issue 8.
Doug Hornbach is the President and Laboratory Director for Lambda Technologies. He has been with the company since 1992. Mr. Hornbach can be reached at dhornbach@lambdatechs.com.
Lambda Technologies
www.lambdatechs.com
Continue to learn from Mr. Hornbach: Attend his educational session at OMTEC 2013 in Chicago.
Residual Stresses: Tools for Optimizing Component Performance
Wednesday, June 12, 11:10 a.m.-12:10 p.m.
The benefits of compressive residual stresses to enhance fatigue strength have long been recognized. The use of low plasticity burnishing (LPB) and compressive residual stresses to enhance the fatigue strength of orthopaedic metals will be discussed. Attendees will learn how to control residual stress in the manufacturing processes, how residual stresses can influence in vivo performance, the treatments can be used to introduce compressive residual stress, how to choose the proper surface treatment for applications and key points to consider when using surface treatments.