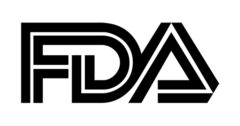
FDA is becoming more and more perceptive when it comes to addressing design controls during an inspection of your Quality Management System (QMS). Let’s go back in time to 1997 when FDA indicated that “starting on June 1, 1997, manufacturers will be inspected for compliance with all the new quality system requirements, including design controls, in the manner described in the inspectional strategy.”
The Transition: As part of the transition program, for a period of one year, although FDA inspected firms for compliance with the design control requirements, the field issued any observations to the manufacturer on a separate design control inspectional strategy report, not on FDA Form 483. The time period from June 1, 1997 to June 1, 1998 was intended to allow both the industry and FDA field investigators time to become familiar with the design control requirements and the enforcement aspects of this new area.
Strategy Reports: The completed strategy reports were reviewed with particular attention paid to clearness of information obtained, the appropriateness of the information collected with respect to the design control requirements, the appropriateness of the questions on the inspectional strategy, the manner in which the investigators are writing out their observations and any requirements that seem to be giving manufacturers a problem, or instances in which there might be misunderstandings as to what the regulation required. Industry was apprehensive.
Important to Note: The design control requirements are not intended to apply to the development of concepts and feasibility studies. However, once it is decided that a design will be developed, a plan must be established to determine the suitability of the design requirements and to ensure that the design that will eventually be released to production meets the approved requirements. FDA investigators will not inspect a device under the design control requirements to determine whether the design is appropriate or “safe and effective.” Section 520(f)(1) (a) of the Food, Drug and Cosmetic Act (The Act) precludes FDA from evaluating the “safety or effectiveness of a device” through preproduction design control procedures. FDA investigators will evaluate the process, the methods and the procedures that a manufacturer has established to implement the requirements for design controls. Based on any information gained during an inspection, if an investigator believes that distributed devices are unsafe or ineffective, the investigator has an obligation to report the observations to the Center for Devices and Radiological Health (CDRH).
Now…Dial up Fourteen Years: The design control requirements of Section 820.30 of the regulation apply to the design of Class II and III medical devices, and a select group of Class I devices. The regulation, in the area of design controls, gives manufacturers just enough rope to hang themselves. The type of design control system and the details of implementation are left for each company to decide based upon the complexity and risks associated with their devices. During an inspection, much attention is paid to these linkages as part of the total process architecture:
- Design and development planning versus what information ends up in the design history file
- Identifying design inputs and then the essential outputs
- Verification work that could eventually end up in the design history file as a formal acceptance activity
- Validating the design from a standpoint of the intended use and user needs
- Controlling design changes before and after commercialization
- Reviewing design results versus the original design plan
- Transferring the design to production while realizing the value of concurrent engineering
- Compiling a Design History File as a basis for the Device Master Record
Design controls are an interrelated set of practices and procedures that are incorporated into the design and development process. This system of checks and balances is not only used to operate on a day-to-day basis, but also as a platform for planning and carrying out an FDA inspection. For example, as a result of these checks and balances, deficiencies in design input requirements and discrepancies between the proposed designs and requirements are made evident in the development process. An initial challenge during any inspection is to ascertain whether or not design controls will increase the likelihood that the design transferred to production has been translated into a device that is appropriate for its intended use. Also, devices are manufactured by companies varying in size and structure, methods of design and development and methods of management. These factors significantly influence how design controls are actually applied and enabled within the confines of 21 CFR, Part 820. Given this diversity, the checks and balances will vary from company to company within this range of compliance and FDA’s approach has become more flexible to accommodate this playing field.
Reviewing the Procedures and the Design Plan: For the designproject selected, the investigator will verify that design control procedures are established and that they, in fact, address the requirements of Section 820.30 of the regulation. Some companies will issue one procedure for all of design controls and work day-to-day from work instructions, whereas other companies will use individual second-level documents to drive each section of design controls. Your choice…here’s the rope. Selling either method is up to the company during the inspection, with a base-line rule of thumb to keep it simple and real.
Reviewing the design plan for the selected project is of the utmost importance to understand the layout of the design and development activities, including assigned responsibilities and interfaces.
Risk Management: Risk management begins with the development of the design input requirements. As the design evolves, new risks may become evident. Because the risk management process is integrated into the design process to ascertain if unacceptable risks can be identified and managed, this facet of the inspection becomes a focal point of every inspection. While the requirement for the conduct of risk analysis appears in Section 820.30(g) Design Validation, FDA investigators will look to make sure that companies do not wait until they are performing design validation to begin risk analysis. Risk analysis should be addressed in the design plan, and risk should be considered throughout the design process. Risk analysis must be completed before and during the design validation phase.
The FDA investigator will most definitively evaluate the firm’s conduct of risk analysis while proceeding through the inspection. Note: When conducting risk analysis, companies are expected to identify possible hazards associated with the design in both normal and fault conditions. The risks associated with those hazards, including those resulting from user error, should then be calculated in both normal and fault conditions. If any risk is deemed unacceptable, it should be reduced to acceptable levels by the appropriate means, for example by redesign or warnings. An important part of risk analysis is ensuring that changes made to eliminate or minimize hazards do not introduce new hazards. By confirming that design inputs were established and verifying that the essential design outputs were also identified, a common bridge to acceptance activities used during post design (e.g. during manufacturing and quality assurance) could be the next line of questioning.
Confirming that acceptance criteria were established prior to the performance of verification and validation activities is usually a topic of discussion. Of course, confirming that risk analysis was performed is an imperative step during an inspection but, more importantly, showing how this analysis ties into possible labeling claims, mitigation activities and process reliability is where your inspection team should spend a concerted effort. Preparing for eventual questions concerned with changes and how they were controlled can lead to whether or not the appropriate verification plans are in sync with the scope and extent of sampling plans, work-in-process inspections and final medical device release. Risk management activities are “salt and peppered” through this phase of the inspection. Your established procedures and the resulting objective evidence should reflect this combination of linked processes in terms of risk. Common tools used by companies to conduct risk analyses include Fault Tree Analysis (FTA) and Failure Modes and Effects Analysis (FMEA).
Design Validation Is Always Challenged: Design validation encompasses the design verification activity and extends the assessment to address whether devices produced in accordance with the design actually satisfy user needs and intended uses. The design validation data should show that the approved design met the predetermined user needs and intended uses. Also, that design validation was completed before commercial distribution of the device. These validation activities will be reviewed to address the needs of all relevant parties (e.g., patient, healthcare worker, etc.) and be performed for each intended use. Note that design validation activities address the design outputs of labeling and packaging, as well. These outputs may have human factor implications, and may adversely affect the device and its use. Lastly, the investigator will try to confirm that the completed design validation did not leave any unresolved discrepancies. All discrepancies must be addressed and resolved by the company being inspected.
The investigator will want to determine if design validation was accomplished using initial production devices or their equivalents. Initial production units, lots, batches or their equivalents are to be used in design validation. They will confirm that such production devices or their equivalents were used by reviewing the design validation documentation. If production devices were not used, the company must demonstrate equivalency to production devices. When the so called “equivalent” devices are used in design validation, the manufacturer must document in detail how the device was manufactured, and how the manufacturing is similar and possibly different from initial production. Where there are differences, the manufacturer must justify why design validation results are valid for production units, lots or batches. The regulation is flexible and does allow for the use of equivalent devices, but the burden lies on the manufacturer to document that the units were indeed equivalent. Process validation may be conducted concurrently with design validation. Production devices used in design validation may have been manufactured in a production run during process validation.
In addition, finished devices must be tested for performance under actual conditions of use or simulated use conditions in the actual or simulated environment in which the device is expected to be used. Samples must be taken from units, lots or batches that were produced using the same specifications, production and quality system methods, procedures and equipment that will be used for routine production. FDA considers this a critical element of the design validation. Manufacturers must also conduct such tests when they make changes in the device design or the manufacturing process that could affect safety or effectiveness as required in the original CGMP in Sec. 820.100(a)(2). The extent of testing conducted should be governed by the risks the device will present if it fails. FDA considers these activities essential for ensuring that the manufacturing process does not adversely affect the device. This aspect of design becomes one of the most visited focal points during an inspection.
Change Control is Not a New Requirement: Product development is an evolutionary process. While change is a healthy and necessary part of product development, quality can be ensured only if change is controlled and documented in the development process, as well as in the production process. Change can put a company on its heels. Investigating these changes will be dependent upon the significance of the change and the risk presented by the device. In preparation for FDA, an internal audit of change management is highly recommended.
All design changes must be verified. Design changes must also be validated unless the performance of only verification can be justified and documented by the firm. Where a design change cannot be verified by subsequent inspection and tests, it must be validated. For example, a change in the intended use of the device will require validation. A comprehensive review of pre-production and a post-production design changes is not uncommon.
Note: Manufacturers are not expected to maintain records of changes made during the very early stages of product development; only those design changes made after the approval of the design inputs need to be documented. Each manufacturer must establish criteria for evaluating changes to ensure that they are appropriate for its designs. The challenge during the inspection will be the documented rationale and the authority behind this strategy.
Design Transfer is an Integral Part of the Design Plan: It is common for the design to be transferred in phases. Production specifications typically consist of written documents such as assembly drawings, inspection and test specifications and manufacturing instructions. Reviewing how the design was transferred into production specifications leads into the construction and review of the Device Master Record where “A” is compared with “A” and “B” is compared with “B” in manufacturing, etc. Both documents are dynamic and alive throughout the lifetime of the medical device. The general requirement for the establishment of procedures to ensure that the design basis for the device is correctly translated into production methods and procedures will be sampled numerous times as the Design History File and Device Master Record are compared in terms of accuracy and control.
Conclusions: Since 1984, FDA has identified lack of design controls as one of the major causes of device recalls. The Safe Medical Devices Act provided FDA with the authority to add pre-production design controls to the device GMP regulation.
As I indicated earlier, the design control requirements are not intended to apply to development of concepts and feasibility studies. FDA will evaluate the process, the methods and the procedures that a manufacturer has established to implement the requirements for design controls. FDA focuses on the most important aspects within each subsystem to determine what the Agency believes is critical and therefore would constitute high risk issues if not properly addressed. Particular attention should be paid to the linkages of these requirements. For example, deficiencies in both design controls and acceptance activities can indicate a major deficiency, because verification control during design versus acceptance activities depends upon a mix of both of these facets of the QMS. Also, if there are problems with one or both, assurances are greatly diminished and possibly compromised.
The review of design controls will cover any design processes performed after June 1, 1997. The manufacturer is not required to retrospectively apply design controls to any stages in the design process that it had completed prior to June 1, 1997, unless changes have been made to the design (including changes in ownership or location where the designed device will be manufactured) after June 1, 1997.
Observations relating to Design Controls placed on the FDA 483 are limited to the adequacy of, and adherence to, the procedures and/or controls established by the company. Observations that concern the adequacy, safety or efficacy of a particular design will commonly not be placed on an FDA 483. Any such concerns will be noted in the Establishment Inspection Report and flagged for review by the Office of Device Evaluation.
Legal, Clinical & Regulatory
John Gagliardi has had success over the past 40 years in the Medical Device and Pharmaceutical industries because of his practical approach to process-orientation and business. He has been actively involved in research and development, quality assurance, training, operations, process architecture, FDA inspections and regulatory affairs. John specializes in building systems in a compliant and business-ready manner. John can be reached via email.
MidWest Process Innovation, LLC
513-573-0085 (phone)
www.midwestprocessinnovation.com