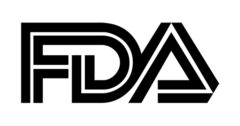
This is the second of two articles dealing with the FDA Warning Letter, in which we’ll look at actual letter excerpts with recommended strategies to respond to FDA in a compliant and effective manner. As discussed in the prior article (See BONEZONE, March 2012), when FDA finds that a manufacturer has significantly violated FDA regulations, it notifies the manufacturer. Responsible officials at regulated manufacturing sites have a legal duty to implement measures to ensure that their products, facilities and operations are in compliance with the law.
When FDA determines that a product is or may become adulterated or misbranded, several actions may be taken, e.g. seizure or detention of a product, injunction of the firm and/or responsible individuals; prosecution of the manufacturer and/or responsible individuals. The actions vary depending upon the degree of danger to the public or willingness of the manufacturer to correct violations.
A Warning Letter may be issued instead of immediately seizing product or obtaining an injunction. The Warning Letter contains a formal advisory that specific sections of the law have been violated and, unless corrective action is taken, FDA is prepared to impose legal and/or administrative sanctions. Unless otherwise indicated, within 15 working days of receiving a Warning Letter, a formal response should be made to FDA.
The following sample includes strategic and tactical steps that you might take in correcting issues following a Warning Letter, in preparation for (possibly) another inspection or ongoing updates to FDA with corrective action(s). The sample includes several sections of the Food, Drug, and Cosmetic (FD&C) Act commonly used in misbranding or adulteration charges. (In this reprint, key words are bolded for emphasis.)
Sample Warning Letter
Department of Health and Human Services
Public Health Service
Food and Drug Administration
10903 New Hampshire Avenue
Silver Spring, MD 20993
December 23, 2011
WARNING LETTER
Via United Parcel Service
Ms.xxxxxxxxxxxxxxxx
President and CEO
Company X, Inc.
Main Street
xxxxxxxxxx, , USA
Dear Ms. xxxx:
During an inspection of your firm located in xxxxxxxxxxxxxx on September 13–16, 2012, an investigator from the United States Food and Drug Administration (FDA) determined that your firm manufactures xxxxxxxxxxxxx, and xxxxxxxxxxxxxxxxxx, Class II Medical Devices. Under section 201(h) of the Federal Food, Drug, and Cosmetic Act (the Act), 21 U.S.C. 321(h), these products are devices because they are intended for use in the diagnosis of disease or other conditions or in the cure, mitigation, treatment, or prevention of disease, or are intended to affect the structure or function of the body.
This inspection revealed that these devices are adulterated within the meaning of section 501(h) of the Act (21 U.S.C. § 351(h)), in that the methods used in, or the facilities or controls used for, their manufacture, packing, storage, or installation are not in conformity with the Current Good Manufacturing Practice (CGMP) requirements of the Quality System (QS) regulation found at Title 21, Code of Federal Regulations (CFR), Part 820.
We received a response from xxxxxxxxxxxxxxxxxxxxxxxx dated September 29, 2011 concerning our investigator’s observations noted on the Form FDA 483, List of Inspectional Observations that was issued to you. We address this response below, in relation to each of the noted violations. These violations include, but are not limited to, the following:
Excerpt One: There was a failure to establish and maintain procedures for implementing corrective and preventative action (CAPA), as required by 21 CFR 820.100(a).
For example: Your firm was unable to provide a copy of the CAPA procedures.
Comment by FDA: We reviewed your firm’s response and concluded that it is not adequate. The Corrective and Preventative (CAPA) Procedures, dated 8/12/2011, are general in nature and did not address all of the requirements listed in 21 CPR 820.100(a). The procedures did not include provisions for analyzing quality audit reports or quality records to identify existing and potential causes of nonconforming product or other quality problems. In addition, the response did not provide evidence of projected implementation of the CAPA procedures.
What is the Issue? Simply put, this company didn’t have a working process in place to address Corrective and Preventive Action(s). When you use the word “establish” in the world of the Good Manufacturing Practices, you are defining the process, documenting your procedure and activities and implementing same. This is the expectation that FDA has when they say “establish and maintain.” Just writing or changing the verbiage in the procedure is not enough. You also have to “put the process into play.”
Steps that might address Excerpt One:
- Determine the root cause for not having this important, core process procedure in place.
- Have a cross-functional team review and dissect the regulation to understand why your present procedure is inadequate. Review by another set of non-biased eyes is not a bad idea before moving forward. Put a plan in place.
- If you don’t have a Quality Review Board (QRB: cross-functional group of individuals that meet periodically to discuss and deal with CAPAs, Complaints, Non-conforming Products, Supplier Issues, etc. – to make, formal risk-based decisions), consider one.
- The process owner for CAPA should write a draft procedure. Have the cross-functional team review and dissect the regulation to understand why this revised procedure is compliant.
- Test the newly-revised procedure using issues in the past for this benchmark exercise and a delta analysis. (Delta: disparity between what is and what ought to be.)
- Start using the new procedure and let the cross-functional team work through disparities, revising as needed.
Excerpt Two: Misbranding and exaggeration of claims…
For Example: …of the advertising pieces we reviewed that misbrand the xxxxxxx follow: (FDA includes samples of exaggerated claims as copied from a billboard)
Comment by FDA: These advertisements fail to reveal material facts, including relevant risk information regarding the use of the Device X and other qualifying requirements for the Device X procedure…these advertisements do not adequately state Device X’s relevant warnings, precautions, side effects, and contraindications. Therefore, the advertisements also misbrand the Device X under section 502(r) of the Act.
FDA requests that xxxxxxxxxxxx Company immediately cease marketing the Device X using advertising that violates the Food, Drug and Cosmetic Act (The Act). Your firm should take prompt action to correct the violations addressed in this letter. Failure to promptly correct these violations may result in regulatory action being initiated by FDA without further notice. Such action could include seizure, injunction, and civil money penalties.
What is the Issue? This is a clear case of FDA noticing advertising claims (on a billboard, no less) and stating that these exaggerated assumptions rendered the medical device adulterated due to misbranding. “Misbranding” applies to false or misleading information, lack of required information, exaggeration of claims, conspicuousness and readability of required information, misleading packaging, etc.
Steps that might address Excerpt Two:
- The Quick Fix: Remove false/misleading labeling from the marketplace (billboards, web sites, sales sheets, brochures, videos, sales presentations, etc.)
- Have a cross-functional team review and dissect the Regulation(s) – 21 CFR, Part 801, for example, and the FD&C Act, to understand why your present labeling is misleading and mislabeled. Determine the root cause and put a plan in place.
- This company has a few options that legitimately present themselves: (1) if the labeling is false or misleading, present substantive evidence to the contrary, (2) if this evidence is non-existent, go back to design controls and conduct tests to verify claims and revalidate for the intended use of the product, (3) take the product off of the market.
- If the decision is made to go back to design controls, the path is clear and evident by challenging every aspect of the previous design.
- Eliminate the whole idea of advertising “FDA Approval”…this is prohibited by dictate.
- Meet with FDA to formally let the district office know about these action plans and the ensuing steps toward compliance.
Excerpt Three: Failure to adequately review the suitability and effectiveness of the quality system at defined intervals and with sufficient frequency according to established procedures to ensure that the quality system satisfies the requirements of 21 CFR 820 and the manufacturer’s established quality policy and objectives, as required by 21 CFR 820.20(c).
For example: Your firm provided a copy of the “Management Review” protocol, dated 09/11/2009, as an example of Sham’s management review procedures. This protocol did not include provisions for appointing a management representative or for specifying the responsibilities of the management representative. In addition, the protocol did not include provisions for the review of quality audit results and other quality data or quality records that will be conducted by your firm.
Comment by FDA: The response did not address this violation. Although your response indicated that xxxx is committed to making each correction as soon as possible, documentation or evidence of the corrections and/or corrective actions for this violation was not provided.
What is the Issue? Management with executive responsibility shall appoint a member of management who will have authority over and responsibility for (1) Ensuring that quality system requirements are effectively established and effectively maintained; and (2) Reporting the performance of the quality system to management with executive responsibility for review.
Thus, the QS regulation requires that management with executive responsibility shall review the suitability and effectiveness of the quality system at defined intervals and with sufficient frequency according to established procedures to ensure that the quality system satisfies the regulatory requirements and the manufacturer’s established quality policy and objectives. The dates and results of quality system reviews shall be documented. This is basically the Regulation as it pertains to Management Review and measuring the effectiveness of the QMS.
Steps that might address Excerpt Three:
- Management must have a face-to-face meeting to formally alert FDA to their commitment and the strategic and tactical action plans that will be put into place to assure ongoing compliance.
- A CAPA initiative must be documented and assignments made to management to fulfill their obligations to their company, as well as The Regulation.
- Have a cross-functional team review and dissect the regulation to understand why you’re your company lacks management commitment.
- The process owner for Management Responsibility should now write a draft procedure. Have a cross-functional team (that includes management with executive responsibility) review the regulation to understand the deliverables. One of the most important responsibilities of management when developing a quality system is to establish its policy and objectives for, and commitment to, quality. Management with executive responsibility shall ensure that the quality policy is understood, implemented, and maintained at all levels of the organization. This means each manufacturer shall establish the appropriate responsibility, authority and interrelation of all personnel who manage, perform, and assess work affecting quality, and provide the independence and authority necessary to perform these tasks.
- Decide when Management Reviews will be held. Schedule a Management Review session.
- Determine what metrics are important to the company from a standpoint of being indicators as to the health and compliance of the company
- Assign process ownership roles to the appropriate individuals to “right the ship”
- Hold an ongoing series of company meetings to “walk-the-talk” with all levels of employees
- Give the FDA District Office official updates as to how this process is working and how commitment is a way of life at your company and not just “lip service.”
John Gagliardi has had success over the past 40 years in the Medical Device and Pharmaceutical industries because of his practical approach to process-orientation and business. He has been actively involved in research and development, quality assurance, training, operations, process architecture, FDA inspections and regulatory affairs. John specializes in building systems in a compliant and business-ready manner. Reach John via email.
MidWest Process Innovation, LLC
513-573-0085 (phone)